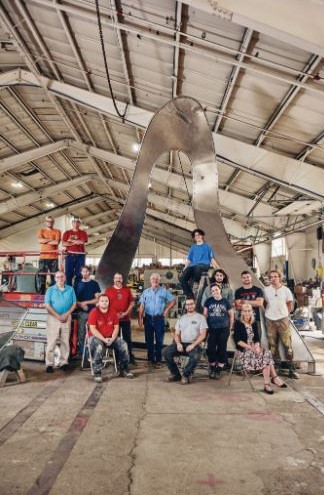
A publication that’s built its brand on illuminating the best of Rhode Island continues their tradition by including an expansive feature on Amaral Custom Fabrications in their November 2019 issue. Rhode Island Monthly writing (John Taraborelli) and photography (Tony Luong) staff visited our facility this Autumn to document what makes our operation regionally, domestically and internationally recognized among members of the art community. Our founder, Paul Amaral guided the visitors through our workspace while recounting his history, explaining technique, introducing them to the team as well as describing current and past projects.
The article dives into how Paul Amaral came to rely on his skilled hands and sharp mind to solve problems. He grew up on a farm in nearby Seekonk, MA where thinking on your feet was essential to making a living. His grandfather shared Paul’s inventive spark, finding solutions to everyday problems with ingenuity. To illustrate this point, Paul shared a memory of his grandfather converting a washing machine into a table saw. Paul summarizes the philosophy of life on his farm, “You didn’t have money to fix the tractor when it broke, so you learned how to fix the tractor. You didn’t hire somebody. You did it yourself.”
A major topic discussed was the Amaral Custom Fabrication’s positive economic impact in the state of Rhode Island. Large scale sculpture fabrication has the ability to migrate the latent specialized work force of shipbuilders and other marine professionals into a new and sustainable industry.
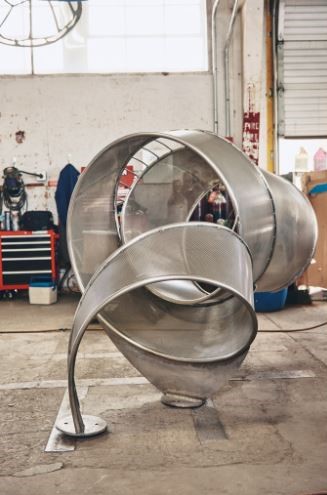
Many of these individuals were left without gainful work opportunities in 1987 when yachtsman Dennis Conner’s grudge resulted in the primary material of manufacturing ships in Rhode Island (aluminum) to be banned from America’s Cup. The Rhode Island shipbuilding institution Merrifield-Roberts reacted with a statement that favored aluminum over modern composites.
Merrifield-Roberts continued to survive after this blow due largely to Paul’s efforts to enter the world of international art. Around the same time that the shipbuilding industry crashed, world-renown artist Claes Oldenburg presented a model of a spoon with a cherry on it and asked if it could be fabricated on a large scale. The result is the iconic Spoonbridge and Cherry, featured in the Minneapolis Sculpture Garden at the Walker Arts Center. After this project, Paul took it upon himself to market Merrifield-Roberts as a sculpture fabrication company. Within several years, the company thrived on sculpture work while marine projects came to a halt.
Paul decided to go into the sculpture fabrication on his own in 1997 when he established his current business: Amaral Custom Fabrications. Since then, Amaral’s reputation as the best sculpture fabricator in the world has only grown – creating large scale pieces by industry giants like Roy Lichtenstein and Keith Haring.
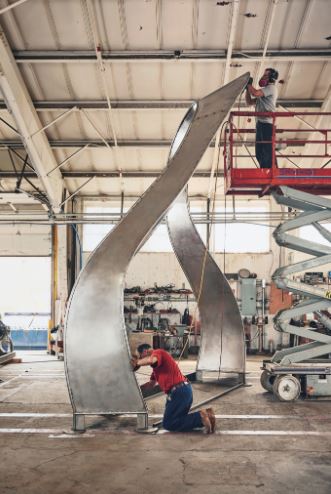
Colorado-based sculptor Gail Folwell describes her experience working with Amaral Custom Fabrications, “…absolutely brilliant. I work with a phenomenal engineer on my pieces. Paul had ideas to make it more cost-effective, more durable. He completely rewrote the book on how these art engineers do things. […] I keep hoping to get new projects that will be an opportunity to work with him again.”
Follow the link below to read Rhode Island Monthly’s entire story.
Meet Paul Amaral, The Art World’s Secret Weapon – By John Taraborelli